This section outlines the distinguishing characteristics of the main types of composting systems that could be suitable for poultry waste composting. Because all systems aim to control the composting process by manipulating temperature, oxygen and moisture, they are variations of a common theme.
The most common type of system is the turned windrow or pile (Figure 5). It is adequate for processing many types of organic wastes, including mortalities. To maintain optimum composting conditions, windrows are managed by turning the mass with either a front-end loader or a specialised windrow turner.
The windrow system is particularly suitable for on-farm composting for several reasons. It is simple and relatively cheap to set up and operate. Windrows need more space than other systems, and in rural areas, likely suitable sites are easier to find for space and buffer distances. On-farm composting operations often have another advantage over commercial operations in urban areas – more time. In windrowing, composting for extended periods helps the process performance.
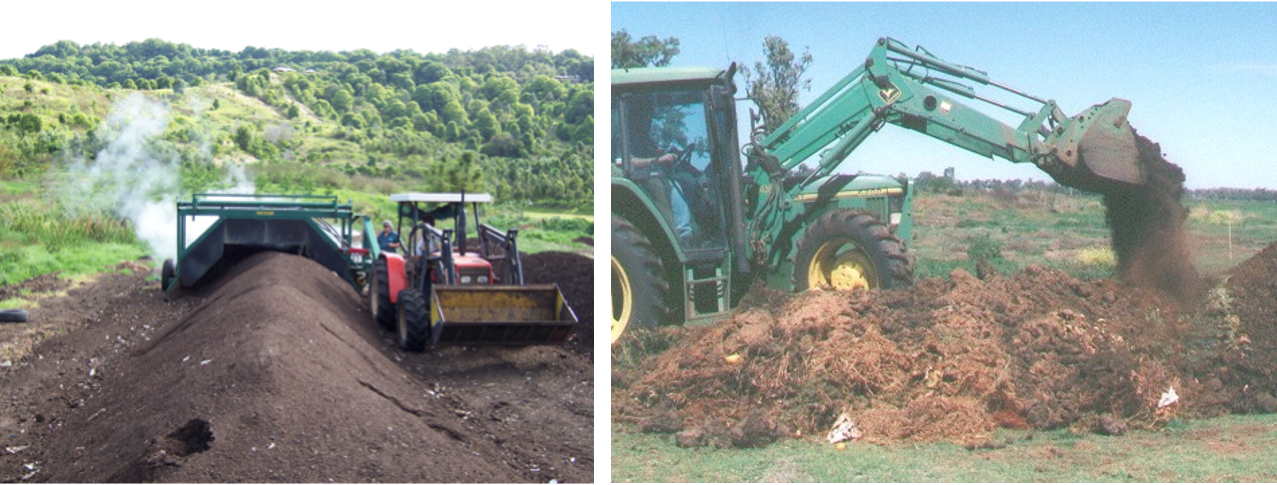
– Low capital and processing costs
– Flexible for a range of wastes; suitable for mortalities, subject to appropriate controls
– Aeration by specialised turner (left) or front-end loader (right)
– Compost can be finished in about 6 weeks (if the compost is to be on-sold to another user, a longer composting period, at least 12 weeks, is recommended)
– Windrows can be outdoors or under a roof
– Care needed for effective control of odour and leachate.
Although mortalities can be composted in open windrows or piles, most poultry operations find that a bin system is ideal for regularly disposing of small quantities of carcasses (Figure 6).
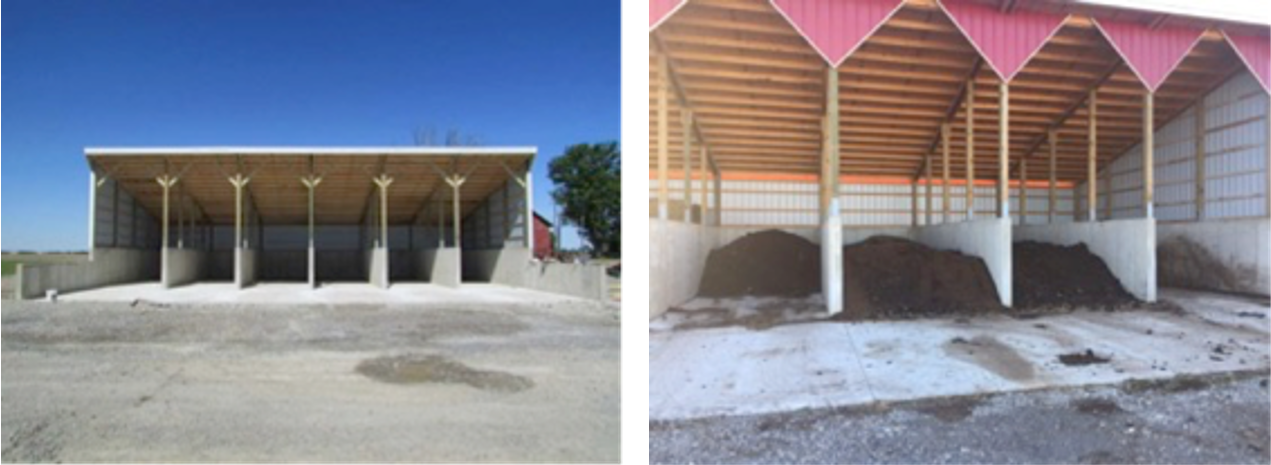
– Most widely used system for mortalities where the bins are progressively filled over 1–2 weeks as carcasses are collected
– Significant capital cost because a roof is usually needed to protect from heavy rainfall
– Low processing costs (simple to operate)
– Aeration by moving compost from one bin to the next in succession
– Compost can be moved out and stored after about 6 weeks composting.
Forced aeration systems (i.e. with fans for aeration) improve process control. They do not necessarily produce compost of higher quality than mechanically turned windrows, but they usually do it faster.
Specialised mortality composting services are also available in some areas. These typically involve a period of composting at the poultry facility, then the process is completed at a commercial facility. The most common example of this approach is offered with the BiobiN™ (Figure 7, left). It is delivered for the poultry farm to fill over an agreed period, after which the bin is exchanged for an empty one. The BiobiN is fully containerised, and aeration is controlled by fan. An odour control system is fitted.
Many variations of fully controlled and scalable containerised composting systems are available commercially. For instance, the Ecodrum system has also been used for poultry mortality composting in Australia. It is an example of a rotating drum system that is designed to improve mixing and aeration during composting (Figure 7, right).
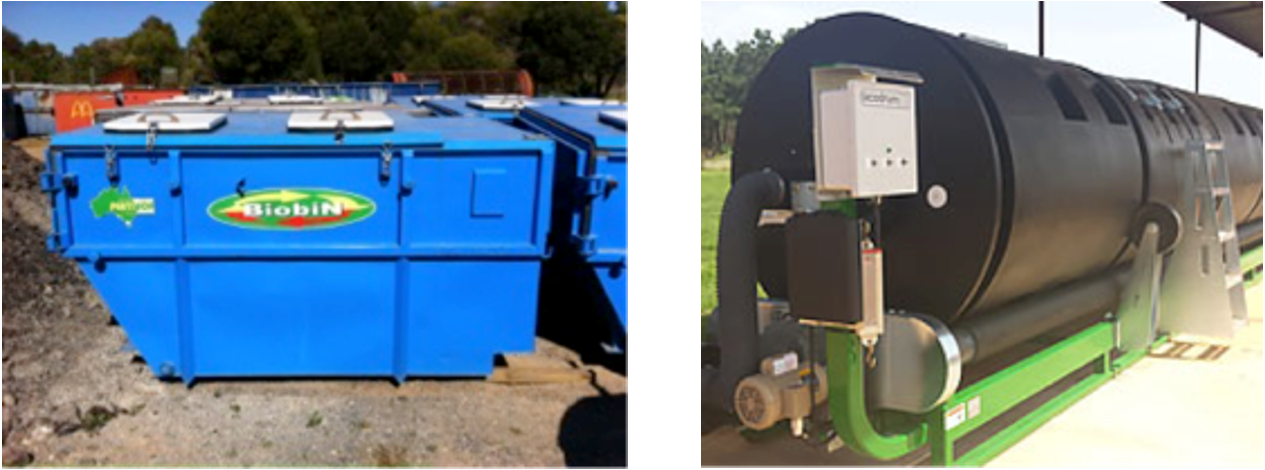
– Often called ‘in-vessel’ composting, these are scalable systems typically with aeration and odour control
– Significant capital cost to buy outright unless the container is leased under a service agreement (as for the BiobiN)
– Medium to high operating costs
– Aeration by fans and, for the Ecodrum, by rotation of the drum.
Highly sophisticated forced aeration systems are commercially available. Though these can be used in on-farm composting operations, the expense can be difficult to justify for all but the largest farm operations. Two examples of such systems are shown in Figures 8 and 9.
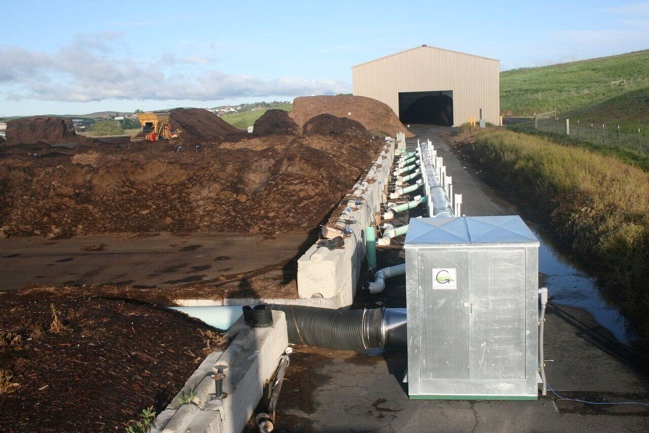
– Medium capital and operating costs
– Forced aeration by fan
– Less flexibility – careful preparation of starting materials is essential
– Some control of temperature and aeration speeds up composting; further curing usually needed.
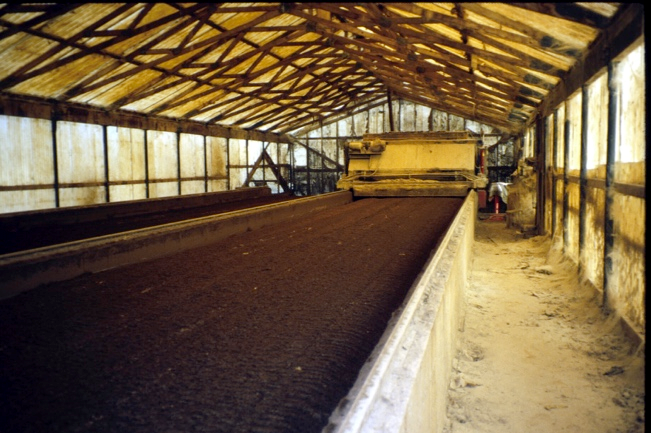
– Medium-high capital and operating costs
– Automated, space-efficient
– Flexible system – both forced aeration and mechanical mixing are used
– Beds are covered in a building or roof
– Odour and leachate control
Retention time in bed or channel: 2–4 weeks; further curing usually needed.
The choice of composting system or technology is generally governed by the following key factors:
– Types of material processed
– Location of the proposed operation and proximity to neighbours (distance, topography, prevailing winds)
– Potential problems from dust, odour or bio-aerosol emissions
– Size of available land and desired processing capacity
– Investment and operating costs.
Although on-farm poultry operations most commonly use a windrow/pile system or bin systems (particularly in North America), farms and agribusinesses near small towns or peri-urban areas may need to consider other options with better biosecurity and odour controls.