Poultry wastes that can be composted include:
– Poultry litter
– Layer manure
– Waste feed
– Daily mortalities
– Dead chicks from hatcheries
– Broken egg waste*.
*Whole eggs should be broken open to ensure that their contents decompose. Although the shell will not decompose, it will contribute a useful quantity of calcium to the mix.
Previously, the desirable specifications for compost mixes to promote optimum composting conditions discussed earlier can be summarised (Table 2).
Table 2. Desirable specifications for composting mixes.
Characteristics | Optimum | Reasonable range |
---|---|---|
Carbon-to-nitrogen ratio (C:N) | 25–30:1 | 20–40:1 |
Moisture content | 50–60% (wet basis) | 40–60% (wet basis) |
Porosity | 35–45% | 30–50% |
Oxygen concentration | >10% | >5% |
Bulk density | <640kg/m3 | |
pH | 6.5–8.0 | 5.5–9.0 |
A mix containing poultry waste can theoretically be co-composted with a whole range of different organic materials (Table 3), but poultry producers are most likely to buy products, such as sawdust and shavings, as per established practice. In any case, poultry waste streams must be blended with clean, high-carbon co-composting material for the following reasons:
- Poultry waste streams all have high nitrogen (N) contents. A high-carbon (C) co-composting material is blended to increase the C:N ratio to within a reasonable range for composting. For poultry composting, a minimum C:N ratio of 20:1 is recommended (Table 2).
- Poultry wastes are odorous and can also represent a biosecurity risk if they are not handled appropriately. Dry poultry litter or other co-composting material (e.g. sawdust) is used to cover these materials to minimise odour and bio-aerosol emissions.
- As mortalities break down, fluids are released. The co-composting material absorbs these fluids and prevents their release into the environment.
Table 3. Physico-chemical properties of a range of organic waste streams.
Feedstock | Moisture | Structure | C:N | %N |
---|---|---|---|---|
Mixed tree and shrub prunings | dry to moist | good | 70–90 | 0.5–1 |
Eucalyptus bark | dry | good | 250 | 0.2 |
Eucalyptus sawdust | dry | average | 500 | 0.1 |
Pinus radiata bark | dry | good | 500 | 0.1 |
Pinus radiata sawdust | dry | average | 550 | 0.09 |
Grass clippings | moist to wet | poor | 9–25 | 2–6 |
Mixed food organics | moist to wet | average | 14–16 | 1.9–2.9 |
Vegetable produce | wet | poor | 19 | 2.7 |
Fruit | wet | poor | 20–49 | 0.9–2.6 |
Fish | moist to wet | poor | 2.6–5 | 6.5–14.2 |
Biosolids | moist to wet | poor | 5–16 | 2–6.9 |
Tannery waste (hair) | dry to moist | average | 3.1–4.3 | 11.7–14.8 |
Mixed abattoir wastes | moist to wet | poor | 2–4 | 7–10 |
Wool scour waste: raw decanter sludge | moist | poor | 13.8 | 0.81 |
Wool scour waste: raw flocculated sludge | moist | poor | 19 | 1.61 |
Grease trap sludges | moist to wet | poor | 0.7–4 | 9–91 |
Flocculated dairy solids | moist to wet | poor | 0.08–8.5 | 5–715 |
Ice cream solids | moist to wet | poor | 1.5–2.2 | 24–41 |
Chicken manure (layers) | dry to moist | poor | 3–10 | 4–10 |
Chicken manure (broilers) | dry to moist | poor | 12–15 | 1.6–3.9 |
Newsprint | dry | poor | 398–852 | 0.06–0.14 |
Paper | dry | poor | 127–178 | 0.2–0.25 |
Wheaten straw | dry | good | 100–150 | 0.3–0.5 |
Seaweed (kelp) | dry to moist | average | 25 | 1.5 |
Sources: Rynk et al. (1992); Handreck and Black (1994); DPI Victoria, unpublished data; Coker (2006). |
Note for Table 3: ‘Structure’ is a descriptive term for the physical property of compost materials. ‘Good’ structure denotes the right particle size distribution to maintain porosity and prevent compaction when stacked in a pile. ‘Poor’ structural material usually has too many fine particles, producing a mix that restricts airflow. This occurs when the pore spaces in the pile are too small to allow free drainage of water, or when a pile slumps under compaction.
Raising the C:N ratio above 20:1 with dry co-composting material can make the mix too dry for composting, so water must be added to compensate. If mortalities are included in the mix, less water is needed than when manure or litter are composted on their own.
Calculating the C:N ratio of a mix made up of more than one feedstock can be a daunting mathematical task for many people. Moisture content must also be calculated simultaneously with C:N ratio to ensure that the mix falls within the recommended range for both attributes. Fortunately, a spreadsheet for the simultaneous calculation of C:N ratio and moisture content is available online from Cornell University (compost.css.cornell.edu/calc/simultaneous.html).
The specifications in Table 2 were developed for commercial composting operations to minimise environmental breaches (e.g. odour emissions), promote thermophilic conditions, and to produce a safe end-product for the consumer. For these specifications, there is a little more flexibility for on-farm composting operations because it should not increase the odour impact of poultry farms. Poultry farms already have challenging odour issues associated with manure and litter. Effective composting should reduce odour emissions, not increase them. Furthermore, in most cases, the end-product is unlikely to be sold because composting on poultry farms is mainly used to manage waste rather than to produce a saleable product.
There is a range of approaches for preparing compost mixes. Mostly, a simple bay-like structure should suffice (Figure 10), but a mixer wagon could produce better results (Figure 11). Recent research shows that a mixer wagon in mortality composting reduces the need for more high-carbon co-composting material (Keaten et al., 2017).
In commercial composting, the usual approach is to prepare a mix that is as uniform as possible for the distribution of particle size, water and nutrients. Because most composting operations on poultry farms will involve at least some mortalities, this principle can be difficult to achieve in practice. As discussed in the next section, mortalities are traditionally layered in a compost pile between alternate layers of poultry litter and/or sawdust (or similar C source). However, more recent research has shown that mortality composting performs better when the carcasses are mixed in a 1:2 to 2:3 ratio (by volume) with poultry litter and/or sawdust or similar C source (Wilkinson et al., 2014).
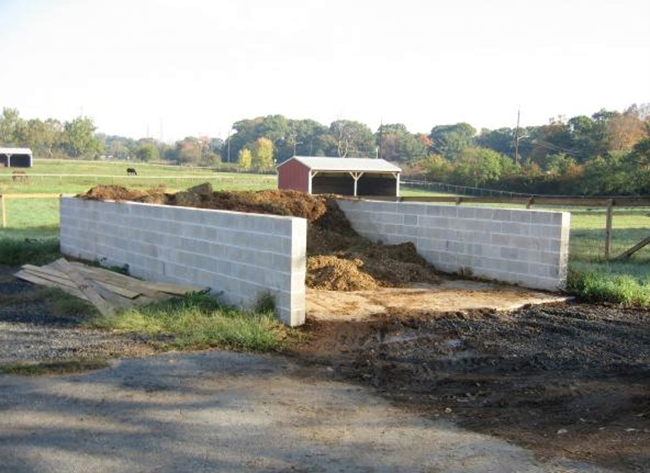
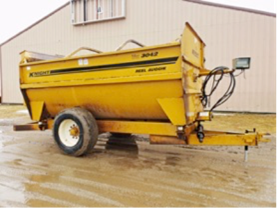
In summary, we can identify the following critical control points for preparing compost mix:
Take a consistent approach to mix preparation – one that has been shown invariably to work. Some trial and error is needed to achieve consistent results, though. Adjusting the composition of the mix may be necessary if there is excessive odour, for example, or where high-risk materials are slow to decompose.
Ensure that highly absorbent, co-composting material is available in the designated mix preparation area to quickly cover high-risk materials, e.g. mortalities, until they can be processed.
When mortalities (or chicks or broken eggs) are placed in the mix preparation area, cover them with at least 1.5× their volume with litter or sawdust (or similar C source). Alternatively, mortalities can be applied directly to piles in the composting area as they are collected (this process is discussed in the next section). In this case, the mix preparation area would be used only to store and prepare other, less hazardous, compost feedstock (such as poultry litter and sawdust).
Mix the material as thoroughly and as uniformly as practicable by loader or mixer wagon before transferring to the composting area. During the mixing process, add water as necessary. In a heterogeneous mix containing mortalities, it can be difficult to practically assess moisture content, but it is usually sufficient to lightly spray the carcasses with water during mixing.
Generally, incorporate high-risk materials into composting within 24 hours. Any material in poor condition (e.g. partly decomposed birds) should be incorporated sooner than that.
Keep equipment (e.g. loader) used in the mix preparation area separate from the curing area. If this is not possible, clean the equipment before using it in the clean area or elsewhere on the farm.
As discussed, there is some flexibility in mix preparation for on-farm composting of poultry waste. With this in mind, key performance criteria for adequate compost mix preparation can be summarised as follows:
– The mix consistently reaches thermophilic conditions quickly (typically within 12 hours) when incorporated into a composting pile.
– The composting process is easily managed with few problems.
– The whole process clearly improves whole-of-site environmental management and biosecurity.