Windrows are horizontally extended piles, the shape and dimensions of which depend on the space available, the feedstock composted (type and quantity), and the equipment available for turning. We will use the terms ‘windrow’ and ‘pile’ interchangeably here because there is little difference in how these heaps are managed in principle.
The length of windrows is limited only by the space available. They are typically 1.5–2m high and 3.5–5m wide at the base. Windrows/piles containing mortalities are typically a maximum of 1.8m high. In high rainfall climates, windrows can be protected from rain with a breathable cover, or they can be formed under a roof. Excessively large heaps can easily overheat, and if they are dry, spontaneous combustion (i.e. compost fires) can occur.
Although large heaps often retain more heat and are more effective in destroying pathogens and weeds relative to smaller ones, odour emissions are common because not enough air can diffuse and aerate the core of the pile. A compromise between pile height and the ability of the pile to retain heat and destroy pathogens and weeds (occurring over 55°C) is needed in managing such piles.
The shape of a pile influences its capacity to absorb water. Creating a concave shape in the top helps water absorption so that rainfall can replenish some of the moisture lost from the compost as steam. In contrast, piles formed into a peak will help to minimise water absorption by shedding water in prolonged wet conditions.
The main reasons for turning compost piles are to move the outside portions of a windrow into the middle and to loosen and fluff the material so that air can move more freely into the windrow. Turning ensures that all parts of a composting mass are exposed to the conditions necessary to eliminate pathogens and weeds. The agitation of composting particles that occurs during turning also stimulates higher rates of decomposition by exposing new surfaces to microbiological attack.
Windrows are turned by a variety of means. Windrow turners are usually more efficient than front-end loaders or excavators because turners are specifically designed for the job. Higher efficiency has a price; a windrow turner is a substantial investment.
PTO-driven windrow turners (Figure 12) are ideal for on-farm composting operations, and they are much cheaper than self-propelled turners (Figure 13).
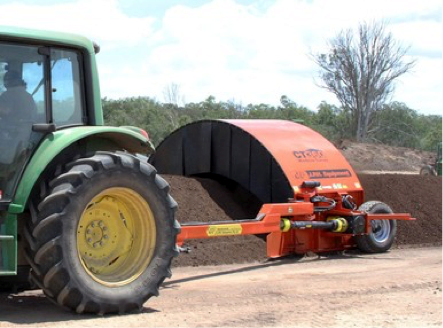
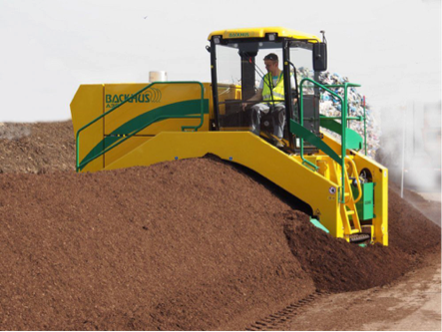
Turning with a front-end loader involves flipping the top of the windrow over just beyond the existing windrow. Then the remaining compost from the base of the windrow is lifted onto the top of the new windrow (Figure 14).
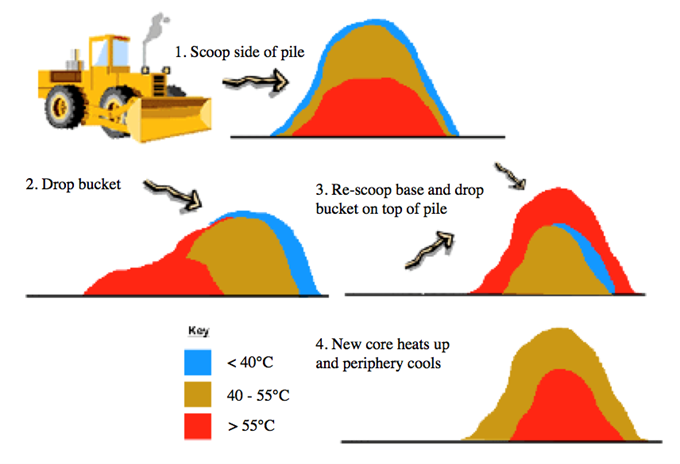
Windrows should be turned when temperatures exceed about 65°C, or when they fall below 45°C, unless the compost has already reached the curing stage. Usually, windrows are turned at least once a week in the first 4–6 weeks, and then less regularly (e.g. fortnightly or less) after that.
Each operation must find its optimum turning strategy because turning is the major cost for operating a windrow system. One advantage of many on-farm operations is that plenty of time and space is available to allow composting for extended periods (e.g. 9–12 months). In this case, relatively few turns are possible provided that appropriate environmental controls are in place.
Turning facilitates the composting process by various means but could also release high peak odour emissions. The turning of windrows may in fact be the most critical activity contributing to odour emissions. Operators should take this into account, and schedule turnings when the wind is moderate, steady and away from sensitive receptors.
Moisture is lost during composting through evaporative cooling and must be replaced by watering. The optimum moisture content for composting is generally considered to be 50–60%. Below about 30%, microbiological activity is severely limited. Water can be added during composting by hose, sprinklers, or soaker hoses. When a windrow turner is used, it can be connected to a water source and added during turning (Figures 15 and 16).
Water must be added slowly to ensure it penetrates the pile rather than running off the surface. Take care to minimise pooling during watering by providing adequate drainage and water (runoff) collection systems. Collected water and leachate should be reused, where possible. If water is discharged to the sewer, land or water, it may need treatment to comply with relevant wastewater discharge regulations.
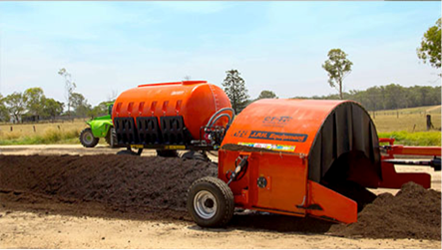
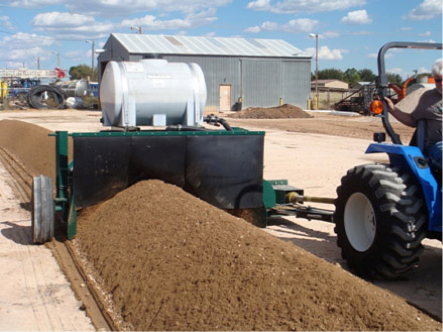