The internal environment in sheds (such as temperature, humidity and airflow) is controlled by the ventilation, design and management (Dunlop 2017). The primary purpose of ventilation is to provide the optimum thermal comfort for chickens, remove moisture and maintain air quality. Effective climate control is essential to manage shed litter moisture content and prevent wet litter. This improves meat chicken welfare and health, which in turn improves bird performance.
Effective climatic control with ventilation and heating systems plays a key role in removing excess water from sheds, and thus avoiding wet litter. Aviagen Inc. (2018) estimated that 10,000 meat chickens (up to 2.3kg) consume about 50,000 litres of water that will be lost to the environment as expired moisture or excreted in droppings. This equate to 100L/m² (or the equivalent of a 10cm depth of water over the entire shed floor) over the course of a grow-out (Dunlop & Stuetz, 2015). Hence, the transfer of moisture out of the litter via evaporation, and an effective ventilation system that removes this excess moisture from sheds, is key to prevent wet litter problems.
The transfer of moisture out of the litter via evaporation, and an effective ventilation system to remove excess moisture from sheds, is paramount to prevent wet litter and the problems caused by wet litter.
Sheds can be naturally ventilated, mechanically ventilated or use hybrid ventilation systems depending on requirements. During natural ventilation, airflow from prevailing wind and natural circulation within sheds is generally sufficient to achieve the desired ventilation levels. However, in hot weather, mixing/stirring fans are sometimes required to maintain chicken thermal comfort. Full mechanical ventilation relies on fans to exhaust air from sheds, and replacement air is drawn from specially placed vents or through evaporative cooling pads. There are two general types of shed construction associated with mechanical ventilation systems:
- Tunnel ventilation (modern style): These sheds have cooling pads at one end, large fans at the opposite end and mini-vents placed along the length of the shed. This design allows air to be drawn across the length of the shed to control air quality and for cooling during summer. Shed air quality is mostly automated by a computer-controlled process, optimising comfort for the chickens during the growth cycle.
- Naturally ventilated (older style): These sheds have curtain walls or wall vents/flaps which can be opened or closed to control air movement and temperature within the shed.
A modern tunnel ventilated shed, as shown in Figure 7, can be operated in several modes depending on the level of ventilation required.
When minimal ventilation is required (e.g. to remove moisture, stale air or ammonia, but minimal/no cooling required), duty fans and mini-vents provide sufficient ventilation. Increased ventilation is achieved by increasing duty fan activity. Mini-vent ventilation ensures an even quantity of fresh air is introduced over the length of sheds, without creating drafts or airspeed (Dunlop & Duperouzel, 2014).
Aviagen Inc. (2018) suggested the use of stirring fans to assist the distribution of warm air throughout sheds when there is minimum ventilation, and when minimum ventilation fans are not in use. Stirring fans effectively bring warm air down to the chicks’ level to help maintain litter and air quality.
When more ventilation is required to ensure chicken thermal comfort (particularly in warmer months), sheds can be operated in full or partial ‘tunnel mode’. This involves the closure of mini vents and opening of tunnel inlets. Tunnel fans draw air from the tunnel inlets through the length of sheds at windspeeds of 3–4.5m/s. A wind chill effect is created by increased airspeed, and the greater quantity of air passing though sheds has a larger capacity to remove heat and humidity depending on the relative internal and external conditions. To ensure adequate air mixing in tunnel ventilated sheds in the roof apex before the air reaches the floor, at least 30Pa of static pressure should be maintained, which causes an airflow through the mini-vents of 3–6m/s.
Additional cooling is achieved by using evaporative cooling pads, which are located at the tunnel inlets, or foggers, which spray a fine water mist throughout sheds (Dunlop & Duperouzel, 2014).
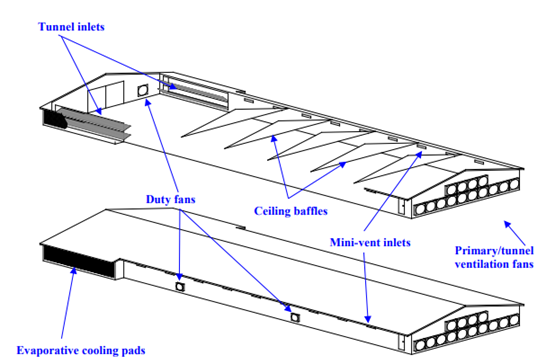
Well-sealed sheds enable better control of litter moisture, reduce running costs and enable better temperature control. To measure air leakage in sheds, the Poultry Housing Tips website has a Poultry house leakage estimating spreadsheet fact sheet (University of Georgia, 2014b) and a Poultry house leakage area calculator (University of Georgia, 2014a).
Watch the Shed tightness, air leakage and water seepage video by AgriFutures Australia (2020) below for more information.
Newer ventilation systems are emerging that are particularly suited to free-range production. These systems operate with inlet and outlet chimneys, and with negative, neutral and positive shed pressure depending on heating, cooling and ventilation requirements, and also with pop-holes. When pop-holes are open, the outlet chimneys are closed, ensuring air is drawn through the inlet chimneys via fans and exhausted out the pop-holes. This system is particularly beneficial for free-range operations in southern Australia that experience prolonged cold and wet periods during winter.
Well-sealed sheds enable better control of litter moisture. The target static pressure for well-sealed sheds is 30–38Pa, and very well-sealed sheds may achieve 62Pa.