Storage of new bedding materials on-farm should be minimised to reduce the potential for contamination. In cases where material needs to be stored due to supply issues, it should be kept in a clean and dry place, preferably in a shed. For material that has high moisture content, it should be aerated to allow it to dry to avoid mould formation. This may need to be forced aeration.
Heating the floor and bedding in the brooding area before placement is as important as heating the air to the correct temperature for the health and comfort of young chicks. This will also avoid condensation in the litter. If the temperature of the floor is below the dew point, condensation will form in the litter. This will leave the litter compromised from day one of the growth cycle, and increase the risk of compaction, which then leads to the formation of cake and slower drying rates. The temperature of the bedding at chick placement should be around 30 °C (±2 °C depending on processor requirements/strain of meat chicken). The Cobb Broiler Management Guide (Cobb, 2018) specifies litter temperatures should be 30–32 °C, while the Ross Broiler Management Handbook (Aviagen Inc., 2018) recommends a temperature range in the litter of 28–30 °C. The temperature of the floor also needs to be within about 3–4 °C of this to avoid condensation within the litter.
Watch the pre-heating litter video below which looks at how cold floors can affect chicks and litter moisture, and how to dry wet bedding before placement (AgriFutures Australia, 2020).
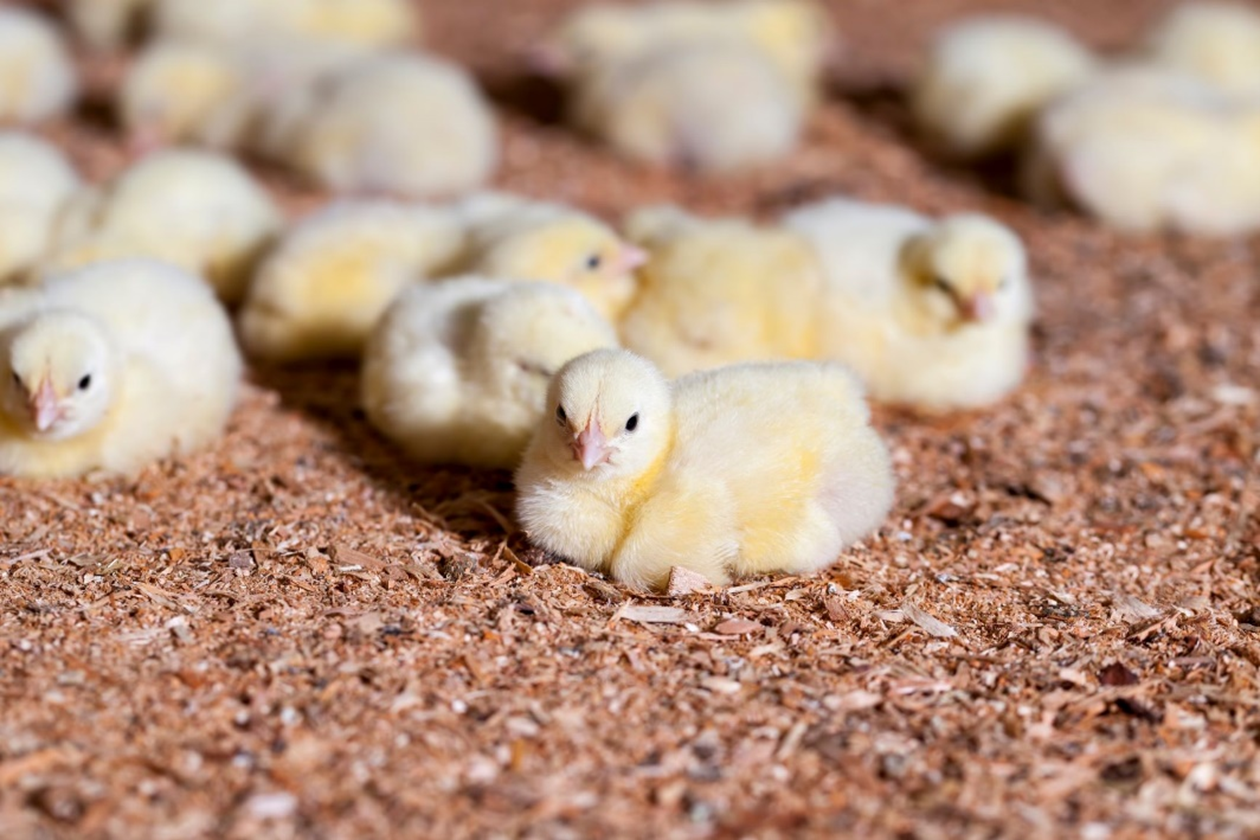
It is important that the minimum ventilation system is started prior to chick placement, particularly if litter reuse is practised. This will remove any excess moisture gases (e.g. ammonia) from sheds. Ritz et al. (2017) recommend heating and ventilating sheds 24–48 hours prior to chick placement. This will help to achieve the correct conditions at placement. Destratification fans, circulation fans or radiant/tube heaters will assist heating the floor and litter to the optimum temperature.
At chick placement, the bedding moisture content should be below 15% (wet basis). If the litter moisture content is too high at chick placement, it can be difficult to rectify once chicks are placed. A hand squeeze test is the simplest method to assess the moisture content. When the litter is dry, it should not form into a stable ball when squeezed and should not feel moist to touch. Conversely, the litter should not be overly dry and dusty. Becoming experienced at making this assessment takes practise. Alternative methods include oven drying and moisture probes. Moisture probes can, however, be inaccurate due to the inconsistent particle size of bedding materials compared with grain products, where moisture probes are commonly used.
At chick placement, perform a hand squeeze test to assess the litter moisture content. Too wet and it will form a stable ball that feels moist and is not easily crumbled.
Sawdust used for bedding can have variable particle sizes and, in some cases, may require sieving/screening to remove larger particles and produce a more consistent product. Large particles in the bedding material will make it more prone to caking, and sharp particles/slivers can cause micro-abrasions to the chickens. Wood shavings are generally a consistent product and do not require additional preparation prior to placement.
Straw and grass-based bedding materials require more pre-treatment prior to placement in sheds. In a survey of Australian growers, Watson and Wiedemann (2018) found several producers have optimised straw bedding by finely chopping and crushing it before use and then turning and mixing (conditioning) as required during the growth cycle. Reducing the particle size makes it more adsorbent and reduces caking problems during the growing cycle. Cobb-Vantress Inc. (2018) recommended wheat straw rather than barley straw for absorptive qualities. They recommend that coarse straw be chopped to lengths of 20mm or less, as coarsely chopped straw tends to cake due to low absorptive qualities during the initial weeks of a growth cycle. Watson and Wiedemann (2018) also found several southern Australian producers add a layer of sawdust over straw to reduce moisture levels and caking during winter. They concluded that more producers across Australia could use straw, as the material is widely available at a competitive cost in most years. However, straw requires additional management (conditioning) to address problems with caking.
Straw requires chopping and/or crushing to lengths that are 20mm or less when using it as a bedding material. Coarsely chopped straw will cake more readily, due to low absorptive qualities, during the first few weeks of a growth cycle. Some producers add a layer of sawdust over the chopped straw to control moisture levels and decrease caking during winter.
Pelletising is an additional pre-treatment option for straw products. This process usually requires straw to be crushed and potentially dried to approximately 13–15% moisture content and cut to 4–5mm in size before pelletising (KMEC Engineering, 2018). Straw is then pressed into pellets under pressure of 115–300MPa and a temperature of 100–130 °C in a straw pellet miller (Whittaker & Shield, 2017). The heat treatment reduces the microbial loads, and the temperature and pressure applied in the pelletising process influence the durability of pellets and physical characteristics. Watson and Wiedemann (2018) found that straw pellets have been used overseas as an alternative bedding material but they are not cost-effective for use in Australia. They gradually break down in sheds throughout the growing cycle, but they are more adsorbent, last longer and cake less than straw. They are also usually less dusty than other bedding materials, however this depends on the manufacturing process and the portion of fines used in the production of pellets, which will vary between pellet manufactures (Watson and Wiedemann, 2018).